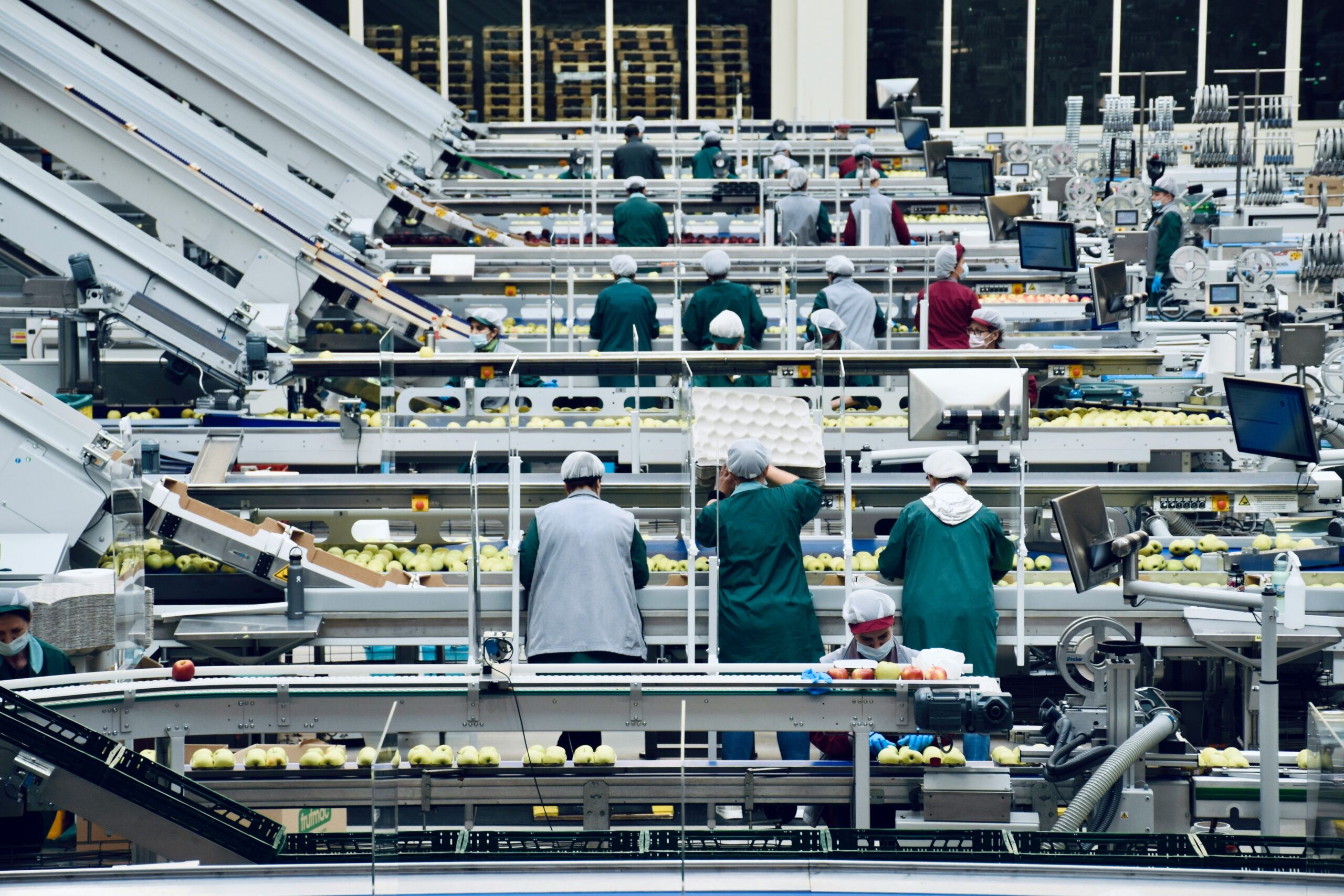
In today’s business world, the ability to operate efficiently while keeping costs down is more crucial than ever. Every organization, no matter its size or industry, faces the challenge of optimizing its operations to ensure long-term success. By implementing innovative process improvements, companies can not only streamline their workflows but also realize significant cost savings. This article examines various strategies that businesses can employ to enhance efficiency and lower costs, ultimately driving both short-term benefits and long-term sustainability.
Assessing and Refining Current Processes
The first step toward process improvement is gaining a clear understanding of how things are currently functioning. Evaluating existing workflows helps identify inefficiencies, redundancies, and bottlenecks that may be slowing down progress. This step involves mapping out processes in detail and understanding the role of each task in the overall workflow.
Once a thorough assessment is complete, businesses can begin refining their processes to eliminate unnecessary steps and improve overall performance. These refinements involve reallocating resources, adjusting team responsibilities, or even adopting new technologies. By improving the core processes that drive operations, organizations can reduce time and costs while ensuring that every step adds value to the end product or service.
Leveraging Automation to Increase Productivity
Automation remains one of the most effective ways to improve efficiency and lower costs. Many routine tasks, such as data entry, scheduling, and inventory tracking, are ideal candidates for automation. By replacing manual processes with automated systems, businesses can reduce the likelihood of human error, accelerate completion times, and free up employees to focus on more strategic tasks.
The use of automation tools also leads to consistent performance. Since machines do not suffer from fatigue, there is less room for mistakes or delays. Additionally, automated systems can operate continuously, providing a level of productivity that would be difficult to achieve manually. Over time, businesses can achieve substantial savings in both time and operational costs, resulting in a better return on investment.
Implementing Lean Practices for Waste Reduction
Lean practices are designed to reduce waste and improve the overall efficiency of business operations. Waste, in this context, refers not just to physical materials but also to time, effort, and human resources. Lean principles emphasize maximizing value by minimizing everything that does not directly contribute to customer satisfaction.
By adopting lean practices, companies can identify areas where waste is occurring and take proactive steps to reduce it. For example, improving inventory management or streamlining production processes can significantly cut costs. Lean also encourages businesses to empower employees to identify and solve problems, creating a culture of continuous improvement. As a result, organizations can achieve higher efficiency while keeping costs to a minimum.
Enhancing Cross-Functional Team Collaboration
Collaboration between departments is crucial for streamlining processes and minimizing inefficiencies. When teams work in silos, they often duplicate efforts, misalign objectives, and overlook opportunities for improvement. To truly optimize operations, businesses must encourage cross-functional collaboration, ensuring that everyone is working toward the same goals.
When departments share information and resources, processes become more transparent and cohesive. This collaboration can also lead to new insights and innovative solutions that might not have been possible if teams had worked in isolation. By fostering a collaborative environment, organizations can enhance workflows, minimize delays, and ultimately reduce costs by addressing issues earlier in the process.
Making Data-Driven Decisions for Smarter Operations
Data is a powerful tool that enables businesses to make informed decisions. With the correct data, companies can gain valuable insights into their operations, identify inefficiencies, and make necessary adjustments. Data-driven decision-making involves collecting relevant data from various sources, analyzing it, and using the findings to guide strategic actions.
For example, sales data can reveal patterns that help businesses forecast demand more accurately, allowing for better resource allocation. Additionally, performance data can identify areas where processes are slowing down, enabling companies to make adjustments that enhance efficiency. By making decisions based on facts rather than assumptions, organizations can optimize their processes and avoid costly mistakes.
Fostering a Culture of Continuous Improvement
Process improvement should be seen as an ongoing initiative, not a one-time event. To truly benefit from innovative process improvements, organizations must create a culture that supports continuous improvement. This culture encourages employees to continually seek opportunities to optimize processes, eliminate inefficiencies, and drive innovation.
When employees are given the tools, resources, and autonomy to improve their workflows, they are more likely to contribute valuable ideas that lead to cost-saving innovations. Regular training, feedback, and performance reviews ensure that employees are aligned with the company’s goals and are continually developing their skills. A culture of continuous improvement enables businesses to adapt to market and technological changes, ensuring long-term sustainability.
Improving Communication Across All Levels
Clear communication is crucial for ensuring that everyone in the organization is aligned and on the same page. Ineffective communication can lead to misunderstandings, delays, and mistakes that can negatively impact operations and increase costs. To optimize operations, businesses must prioritize transparent communication at all levels of the organization.
This means ensuring that team members have access to the information they need to do their jobs effectively and that management provides clear guidance on priorities. Whether it’s through regular meetings, internal memos, or collaborative platforms, consistent communication helps keep everyone informed and focused on achieving common goals. By improving communication, organizations can reduce inefficiencies, minimize errors, and foster a more productive and cost-effective work environment.
Regularly Reviewing and Refining Processes
To maintain efficiency and cost-effectiveness, businesses must regularly review their processes to ensure ongoing improvement and optimization. The needs of the industry, market conditions, and technology are constantly changing, and processes that were effective in the past may no longer be as relevant today. Regular reviews allow companies to stay agile and ensure their processes remain optimized for current conditions.
During these reviews, businesses should assess whether their existing processes are still serving their intended purpose or if adjustments are needed. The review process can also uncover new opportunities for improvement, ensuring that the organization continues to move forward with optimized operations. By creating process evaluation as a regular part of operations, businesses can sustain improvements and continue to reduce costs.
Optimizing operations through process improvement is crucial for businesses seeking to enhance efficiency and lower costs. Whether it’s automating routine tasks, adopting lean practices, fostering collaboration, or using data-driven insights, the key to success lies in continually refining processes to meet the changing needs of the business.
By embracing these strategies, organizations can not only improve their internal operations but also position themselves for sustainable growth and success. With a focus on continuous improvement, businesses can create more efficient workflows, enhance productivity, and drive long-term cost savings.